Aluminium is a versatile material widely used in various industries due to its lightweight and strength. To ensure its longevity and performance, applying a protective coating is essential. Anodizing is a highly effective method that not only protects aluminium from corrosion but also enhances its aesthetic appeal.
This electrochemical process increases the thickness of the natural oxide layer on the metal surface, making it more durable. Anodized aluminium is resistant to wear and abrasion, making it ideal for both indoor and outdoor applications. Choosing the right protective coating ensures your aluminium products remain in top condition for years.
Types Of Coatings
Aluminium is a popular material due to its light weight and strength. But it can corrode easily without protection. Choosing the best protective coating is crucial. There are different types of coatings available. Each has its own benefits and drawbacks. This article will explore the types of coatings for aluminium.
Anodizing
Anodizing is a common method to protect aluminium. It involves an electrochemical process. This process increases the thickness of the natural oxide layer on the surface. The result is a durable and corrosion-resistant coating. This method also improves the appearance and hardness of the aluminium.
There are several benefits of anodizing:
- Enhanced durability
- Better corrosion resistance
- Improved aesthetics
- Non-toxic and environmentally friendly
Anodizing is suitable for many applications. These include architectural structures, consumer electronics, and automotive parts. The process can also be combined with dyeing. This allows for a variety of colors and finishes. This versatility makes anodizing a popular choice for many industries.
Powder Coating
Powder coating is another effective way to protect aluminium. This method uses a dry powder that is applied to the surface. Then, the coated item is heated in an oven. The powder melts and forms a smooth and durable finish. This coating is resistant to chipping, scratching, and fading.
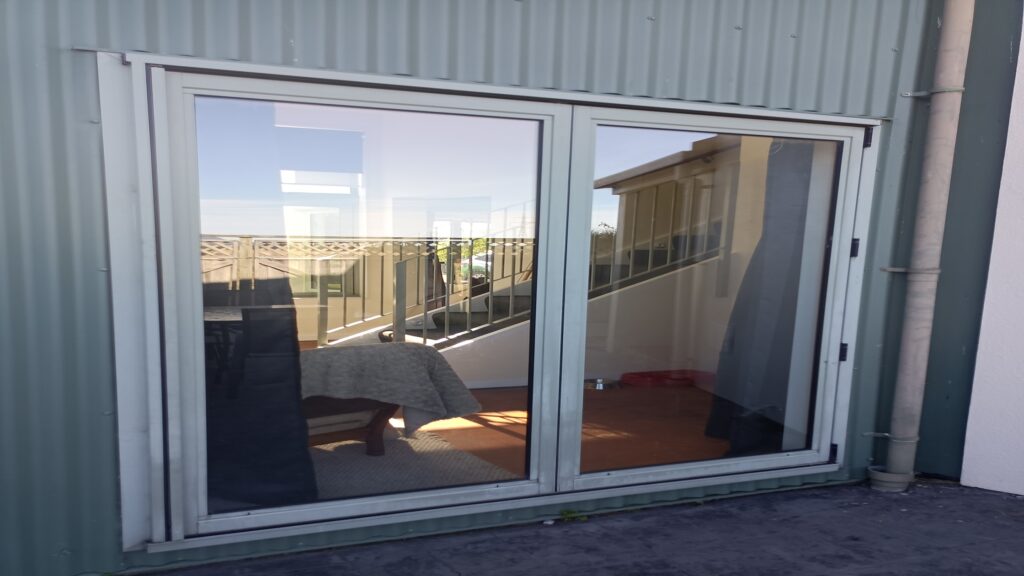
Advantages of powder coating include:
- Strong and long-lasting finish
- Wide range of colors and textures
- Environmentally friendly
- Cost-effective
Powder coating is used in many industries. Common applications include furniture, automotive parts, and household appliances. This method is also known for its eco-friendly properties. Unlike liquid paints, powder coating does not release harmful solvents into the air.
Liquid Paints
Liquid paints are a traditional method for coating aluminium. This involves spraying or brushing a liquid paint onto the surface. The paint then dries to form a protective layer. Liquid paints can offer a smooth finish and a variety of colors.
Benefits of liquid paints include:
- Wide range of colors and finishes
- Easy to apply
- Suitable for complex shapes
Liquid paints are often used in automotive, aerospace, and construction industries. They are especially useful for items with complex shapes. The application process allows for a uniform and smooth finish. Despite some limitations, liquid paints remain a popular choice.
Benefits Of Anodizing
Choosing the best protective coating for aluminium is important. Anodizing is one of the most popular choices. This process offers several benefits, making it a top pick. Let’s explore the benefits of anodizing in detail.
Durability
Anodizing aluminium makes it much stronger. The surface becomes harder than untreated aluminium. This is because the anodizing process creates a thick oxide layer. This layer is resistant to scratches and everyday wear.
Here are some key points about its durability:
- Increased surface hardness
- Resistant to abrasion and scratches
- Longer lifespan of aluminium products
This enhanced durability is perfect for items that face heavy use. Examples include cookware, electronics, and automotive parts. The added strength ensures these items last longer.
Corrosion Resistance
One of the biggest advantages of anodizing is corrosion resistance. The process creates a protective oxide layer on the aluminium. This layer shields it from moisture and harsh chemicals. It makes anodized aluminium ideal for outdoor applications.
Consider these benefits:
- Protection against rust
- Resistant to chemical damage
- Ideal for marine and outdoor environments
For example, anodized aluminium is used in marine equipment and building facades. These applications need materials that can withstand harsh weather. Anodized aluminium meets these needs perfectly.
Advantages Of Powder Coating
Aluminium is a popular material due to its light weight and strength. To keep it in top shape, it needs protection. Powder coating is one of the best ways to protect aluminium. This method offers many benefits. Let’s explore the advantages of powder coating.
Finish Variety
Powder coating provides a wide range of finishes. It can mimic the look of other materials. You can choose glossy, matte, or satin finishes. This allows for creative freedom.
Here are some options:
- Glossy Finish: Shiny and reflective
- Matte Finish: Smooth and non-reflective
- Satin Finish: Soft sheen, in between glossy and matte
Each finish has its own charm. Glossy finishes are great for a shiny look. Matte finishes give a modern touch. Satin finishes balance both. This variety ensures that your aluminium looks just the way you want.
Environmental Safety
Powder coating is good for the environment. It does not use harmful chemicals. Unlike traditional paints, it is free from volatile organic compounds (VOCs). These compounds can harm the air.
Benefits include:
- No VOCs: Keeps the air clean
- Minimal Waste: Excess powder can be reused
- Energy Efficient: Less energy needed for curing
This method ensures that the environment stays clean. Less waste is produced, and the process is energy efficient. This makes powder coating a top choice for eco-friendly protection.
Liquid Paints Vs. Other Coatings
Choosing the best protective coating for aluminium is crucial. Aluminium is used in many industries because of its durability and lightweight nature. Protective coatings help to shield the metal from damage, corrosion, and wear. Liquid paints and other coatings each have unique benefits and drawbacks.These can guide you to make the best choice for your needs.
Application Ease
Liquid paints are often easier to apply. They can be sprayed, brushed, or rolled onto the surface. This makes them versatile for different projects.
Here are some key points:
- Spraying allows for a smooth, even coat.
- Brushing is good for small areas or touch-ups.
- Rolling works well for large, flat surfaces.
Other coatings like powder coatings need special equipment. Powder coating involves applying a dry powder and then baking it. This process can be more complex and requires more time.
Here’s a comparison table:
Coating Type | Application Method | Ease of Use |
Liquid Paint | Spray, Brush, Roll | Easy |
Powder Coating | Electrostatic Spray, Baking | Complex |
Liquid paints can be applied without much training. Powder coating often needs trained professionals. This makes liquid paints more accessible for small projects or DIY tasks.
Cost Factors
Cost is a significant factor in choosing a protective coating. Liquid paints are generally cheaper upfront. They do not require expensive equipment.
Here’s a cost breakdown:
- Liquid paint: Lower initial cost
- Powder coating: Higher initial cost due to equipment
Long-term costs also matter. Liquid paints may need more frequent reapplication. This can add to maintenance costs over time. Powder coatings are more durable and may last longer. This could save money in the long run.
Here’s a summary table:
Coating Type | Initial Cost | Long-term Cost |
Liquid Paint | Low | Higher due to maintenance |
Powder Coating | High | Lower due to durability |
Choosing the right coating depends on your budget and project needs. For small, low-budget projects, liquid paints are a good choice. For long-term, durable protection, powder coatings may be better.
Factors To Consider
Choosing the best protective coating for aluminium involves understanding several key factors. Aluminium is a versatile and durable material, but it needs protection to maintain its appearance and structural integrity. Factors like environmental exposure and the desired finish play crucial roles in determining the best protective coating. This blog post will explore these factors to help you make an informed decision.
Environmental Exposure
Environmental exposure significantly impacts the choice of protective coating for aluminium. Different environments present unique challenges that can affect the longevity and effectiveness of the coating.
Outdoor environments expose aluminium to various elements like rain, sun, and pollution. In these conditions, a coating with UV resistance and water repellence is essential. These coatings prevent corrosion and fading. For industrial settings, chemicals and abrasives are common hazards. A protective coating must provide chemical resistance and abrasion protection. This ensures that the aluminium remains intact despite harsh conditions.
In marine environments, saltwater exposure is a major concern. An anti-corrosive coating designed for marine use will protect the aluminium from saltwater damage.
- Outdoor Environments: UV resistance, water repellence
- Industrial Settings: Chemical resistance, abrasion protection
- Marine Environments: Anti-corrosive properties
Desired Finish
The desired finish is another critical factor in selecting a protective coating for aluminium. Different finishes offer various aesthetic and functional benefits.
Glossy finishes provide a shiny and reflective surface. They are often used for decorative purposes. These finishes enhance the visual appeal of aluminium structures and products.Matte finishes offer a subdued and non-reflective look. They are ideal for applications where glare reduction is important. This finish is also good at hiding scratches and imperfections.
For functional purposes, textured finishes add grip and reduce slipperiness. This is particularly useful in flooring and handrails.
- Glossy Finishes: Shiny, reflective, decorative
- Matte Finishes: Subdued, non-reflective, hides imperfections
- Textured Finishes: Adds grip, reduces slipperiness
Maintenance Tips
Aluminium is a popular material due to its durability and lightweight properties. To maintain its shine and strength, applying a protective coating is essential. The right coating can prevent corrosion and extend the lifespan of aluminium surfaces. Here are some maintenance tips for keeping your aluminium in top condition.
Cleaning Methods
Regular cleaning is crucial for maintaining the protective coating on aluminium. Dust and grime can wear down the coating over time.
Use a soft cloth or sponge with mild soapy water. Avoid abrasive cleaners which can scratch the surface.
- Rinse the aluminium thoroughly with clean water.
- Dry the surface using a soft towel to prevent water spots.
- Inspect for damage or signs of wear after cleaning.
If stubborn stains are present, a mixture of vinegar and water can be effective. Apply gently with a soft cloth. Always test a small area first to ensure no damage occurs.
Reapplication Frequency
Regular reapplication of the protective coating ensures long-lasting protection. The frequency depends on environmental factors and usage.
For areas exposed to harsh conditions like coastal regions, reapply every 6 months. In less harsh environments, a yearly reapplication is usually sufficient.
Environment | Reapplication Frequency |
Coastal areas | Every 6 months |
Urban areas | Every 12 months |
Rural areas | Every 18 months |
Always follow the manufacturer’s instructions for the specific coating product. Proper maintenance ensures your aluminium remains protected and looks its best for years.
Frequently Asked Questions
What Is The Best Coating For Aluminium?
Epoxy coatings are the best for aluminium. They offer excellent protection against corrosion and wear.
How Do You Protect Aluminium From Corrosion?
Apply a protective coating like anodizing or epoxy paint. These methods create a barrier against moisture and chemicals.
Can Aluminium Be Powder Coated?
Yes, aluminium can be powder coated. This process provides a durable, protective finish that resists corrosion and wear.
What Is Anodizing Aluminium?
Anodizing is an electrochemical process. It increases the thickness of the natural oxide layer on the aluminium surface.
Why Is Epoxy Coating Recommended For Aluminium?
Epoxy coating is recommended because it provides a strong, durable layer. It resists moisture, chemicals, and physical damage.